Today, in this post, we are going to see what is boiler deaerator, and deaeration tank, their types, and their working principles.
Utilities play a vital role in plant operation as utilities help to maintain process-required temperature, pressure, and other process parameters. Previously we had discussed the cooling water utility in Cooling Tower efficiency calculation article.
Among several utilities, steam is one of them and is a basic requirement for the plant. We can find a number of uses of steam, like the generation of electricity, use in the process to achieve high reaction mass generation, use in a steam jet ejector to create a vacuum, in VAM chiller and many more.
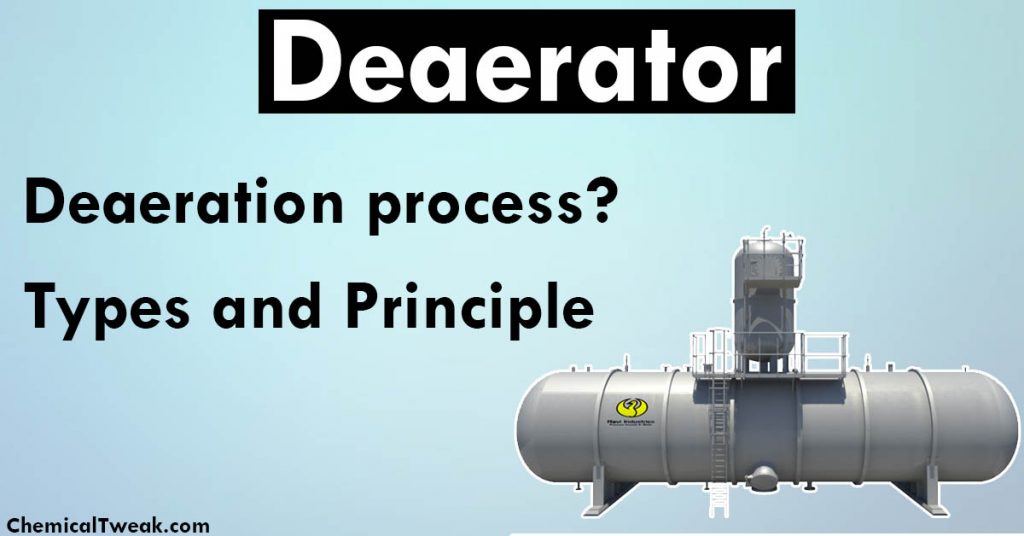
Now we understand why steam is important for the plant. Steam is generated using a boiler and boiler feed water is used as a feed in the boiler to generate steam. Unlike any other equipment, it is important to control the quality of feed and similarly, feedwater it is essential for boiler operation.
Feedwater is recycled for the boiler operation for the generation of steam and this has to be treated as feedwater contains oxygen and other gases which may result in corrosion of tubes, scaling of the inner surface, premature tube failure or excessive feedwater leaks and many more.
Table of Contents
Boiler Feedwater – Why Treat Boiler Feedwater?
The boiler is used to generate electricity and hence it is used in the chemical industry and power plant. Process water, recycle boiler water, vapor condensate are used as boiler feedwater. Feedwater contains oxygen maybe by exposure to the atmosphere or by leaks in tubes of boiler.
Along with oxygen, some other gases also get dissolved in the water. If this water is fed to the boiler then present oxygen and carbon dioxide which turns into carbonic acid at high-temperature causing corrosion to boiler tubes and other parts of the boiler. Hence boiler feedwater needs to be treated prior to feeding into the boiler.
Methods to treat boiler feedwater
There are two methods that one can use to treat boilerfeed water
- Physical methods
- Chemical Methods
1 – Chemical Methods
In this method, chemicals are used to treat boiler feedwater. Chemicals are Boiler Oxygen Scavengers, dosed in the boiler feedwater which removes dissolved oxygen. Oxygen scavenger chemicals are dosed into the system or into the tank used as a feeding tank / storage tank for boiler feed. It is recommended to dose chemicals as back as possible from the boiler for taking maximum effect.
2 – Physical Methods
The physical method means physical treatment given to the boiler feedwater. This is another method which serves the purpose of removing dissolved oxygen from water using equipment which is an aerator.
What is the deaeration process? – how does a deaerator work
To treat boiler feedwater, an equipment aerator is used prior to feed water to the boiler, which helps in removing dissolved oxygen from the water. An aerator is widely used in the chemical industry and power plants in where the boiler is used to generate steam.
The purpose of installing a deaerator is to remove the oxygen dissolved in water prior to use as feed in the boiler.
Principle of Deaerators – Deaeration tank
Aerators work on two principles, and those are Hendry’s Law and Gas solubility. let us discuss the working principle of deaerators in detail and how there are applied the deaeration process.
1. Hendry law
Henry’s law is a gas law that states that the amount of dissolved gas in a liquid is proportional to its partial pressure above the liquid. The proportionality factor is called Henry’s law constant.
C = K P
Where, C is the concentration of a dissolved gas
K = Henry’s Law constant
P = partial pressure of the gas
2. Inverse Solubility of Water
Inverse solubility of water states that as the temperature of water increases, the dissolved oxygen content within the water is decreased. Hence in the deaeration process, we dose steam to increase boiler feed water temperature, which leads to a decrease in solubility of gases and removal of oxygen and other dissolved gases.
Types of Industrial steam deaerator
There are two types used in industries also known as Industrial steam deaerators.
- Tray types
- Spray-type
Tray types Deaerator
Tray type also known as Cascade Type, are a type of industrial deaerator, contains perforated trays at the top section known as a dome from where feedwater is the inlet. The bottom section is a storage tank where the boiler feedwater is stored. As shown in the figure, inlet feedwater is passed over the perforated tray which helps to distribute feed evenly.
Steam is feen below the trays to strip out and remove dissolved oxygen from the water. Perforated trays help to increase the residence time/contact time of feedwater and steam. After passing through steam, feed is collected into the horizontal water storage tank. In the storage tank, steam is passed through the sparger pipe which further heat the water and remove the leftover dissolved oxygen.
Steam will increase the temperature of the water and helps to reduce the solubility of oxygen and it gets purge out through the Air vent, also known as a deaerator vent. Now the stored deaerated boiler feedwater is pumped to the boiler through pumps.
Spray-type Deaerator
Spray Deaerator is another type in which the boiler feedwater that contains oxygen and other gases is pre-heated in E section using steam. Ther is baffle placed between the preheating and deaeration section,s which increases the retention time. As the feedwater is preheated and the level rises, to flows to the deaerated section.
In the Deaeration system, low-pressure steam is passed into the system through the spray nozzle in the feed water to further increase the temperature. Due to the rise in temperature, the solubility of oxygen is decreased, and liberated gases get purge our from the air vent. Now, this deaerated boiler feedwater is then pumped into the boiler.
FAQ (types of deaerator)
1. What is the function of deaerator?
The function is to treat boiler feed water. It removes oxygen dissolved in water prior to use as feed in the boiler. Additionally, it acts as a storage for feed water in case of failure of supply of water from the reservoir
2. Why are deaerators placed at height?
Net positive suction head available is required by the feedwater pump which are placed typically on the ground level and hence to provide that, they are placed at a height.
2. What are the types of Deaerator?
Industrial deaerators are of two types,
1. Tray types
2. Spray type
Wrapping Up
This was a detailed tutorial on What is deaerator? and how do a deaertors work and the working principle. If you have any doubt regarding the topic, then feel free to use the comment section; we will help you with your doubts.
In case you want us to cover any topic related to chemical engineering or industrial safety do commend the topic and also don’t forget to check other articles like types of distillation where we had covered details regarding distillation types.